Full Range Korean Vehicles Wheel hub Solutions
Trusted by dozens of world-class brands and organizations of all sizes
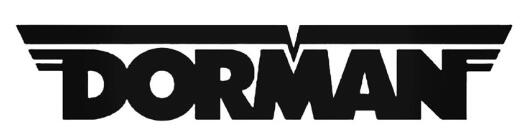
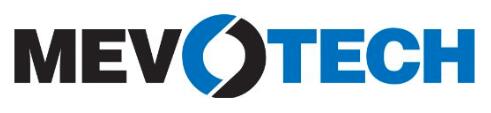

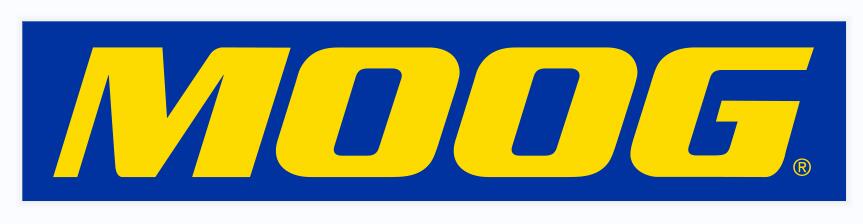
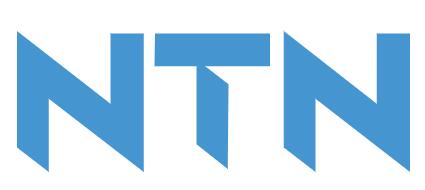

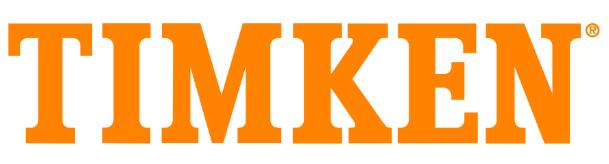
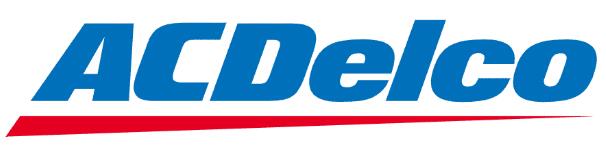
Who We Are
Wheel bearing & hub assembly manufacturer
Wana Auto Parts Co., Ltd owned this site wheelhubfactory.com. We manufacture high-performance wheel bearings and hub assemblies. Our factory is located in Yuhuan City, the biggest auto chassis parts production base in China, and all the products are under strict quality control before delivery. Our experienced technicians are always ready to provide the necessary services for you.
We're No.1 Wheel Hub Factory
- Over 2800 models in range
- $20 million annual output
- Capacity 10,000 sets per day
Our Advantages
From Roughs to Assemblies Are All Made by Us
Extreme cost control, strict quality control, rich market experience, and good communication are incomparable to any factory.
2 years or 80,000 km warranty.
Korean vehicles' wheel bearing and hub assembly
All Korean vehicles here include KIA, HYUNDAI, DAEWOO, SSANGYONG, etc. We will continue to develop new products; anything you can’t find elsewhere, we can develop for you, and we bear all the development costs ourselves.
Durable Packaging
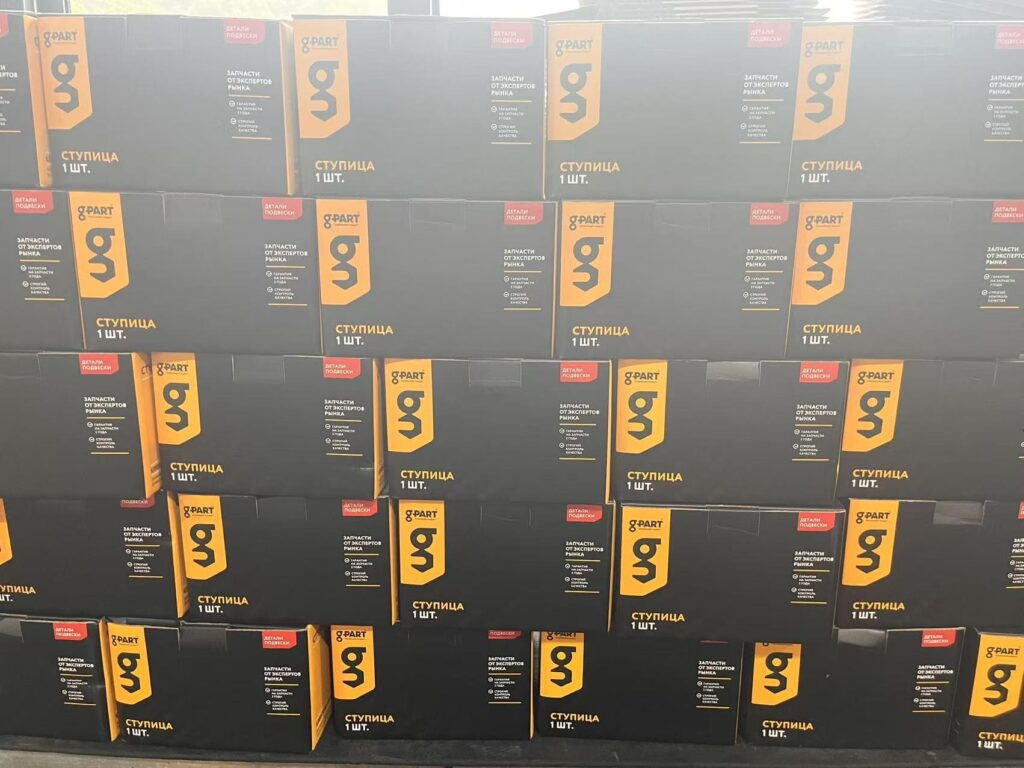
Our original reinforced packing method can effectively protect ABS sensors and bolts from damage during transportation
Our Wheel Hubs Production Process
The main process flow of our components (inner and outer flanges and inner rings.)
Inspection & Testing
Full inspection is done at each step of the production process, and faulty parts are not passed on to the next step.
We have a complete set of instruments to test all sizes of the most critical components, including a roundness measuring instrument, profilometer, rough meter, precision altimeter, length measuring device, angle measuring tool, residual magnetometer, etc.
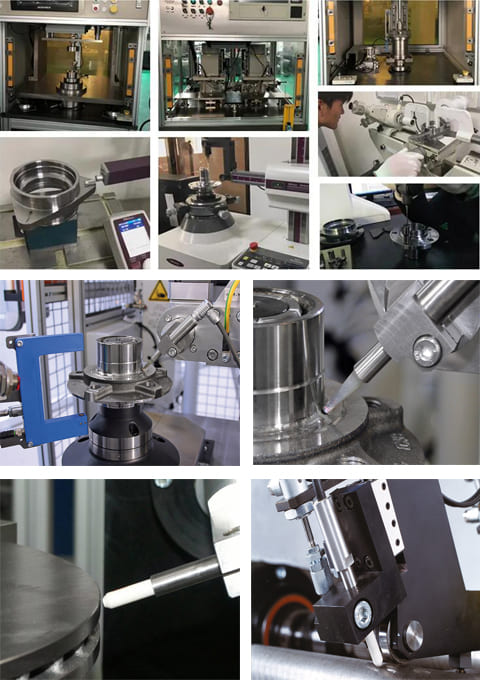
Our Wheel Hub Performance Test Equipments
Not all wheel hubs are the same; let’s talk about our stand-out.
ABS sensor testing
The main purpose of the ABS is to prevent the wheels from locking up, which can lead to a loss of steering control and traction, especially on slippery surfaces. By constantly monitoring the wheel speed and sending this data to the control unit, the ABS sensor helps maintain optimal braking performance, ensuring a safer and more stable driving experience.
Therefore, for these essential safety parts, each product must be fully inspected; any one failed product will not flow into your large goods.

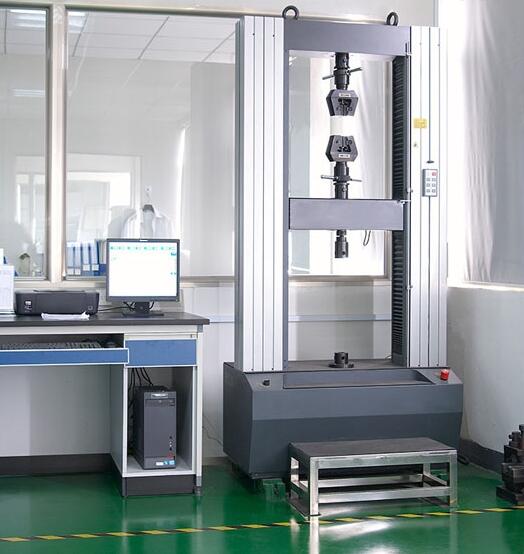
Bolts tensile strength testing
The tensile strength of a bolt is a measure of its ability to resist pulling or tensile forces without breaking. The bolt tensile strength tester is used to determine the maximum amount of tension that a bolt can withstand before it breaks. This information is essential in ensuring that the bolts used in the assembly of wheel hubs are strong enough to withstand the stresses and loads placed on them during operation.
By testing the tensile strength of bolts used in wheel hub assemblies, the bolt tensile strength tester helps to ensure the safety and reliability of the vehicle. Weak or faulty bolts can cause the wheel to come loose while driving, leading to a potentially catastrophic accident.
The bolts we use have a tensile strength of over 1000 Nm, far beyond the competition in the market.
Wheel hub life testing
A life tester in the wheel hub field to test the lifespan and reliability of wheel hub bearings under different loads and speeds. It simulates the fatigue and wear of the bearings under actual operating conditions and provides data to assess their lifespan and reliability. By subjecting bearings to life testing, the expected lifespan of the bearings in actual use can be determined, which helps manufacturers design more durable and reliable wheel hub components, thereby improving vehicle safety and performance.
A low-temperature test has been added to our life tester to test the changes in grease at temperatures as low as -40 degrees to help us use better grease for wheel unit used in various extreme environments.

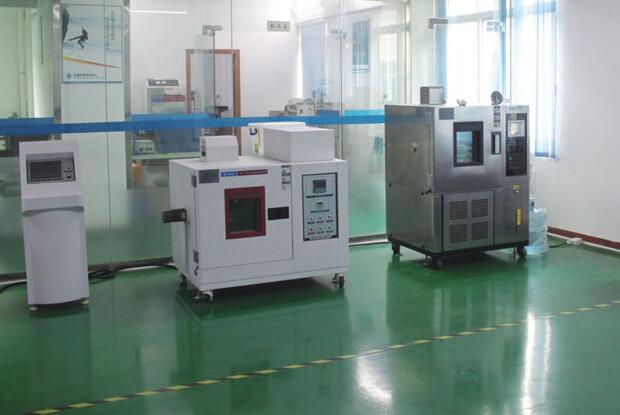
Clay water endurance testing
A clay water endurance testing machine in the wheel hub field is used to test the water resistance and durability of wheel hub components. This machine simulates real-world conditions where wheel hubs may be exposed to moisture, mud, and other contaminants that can compromise their performance and longevity.
The wheel hub is rotated during the test while submerged in a clay water mixture. This mixture mimics the corrosive and abrasive nature of real-world contaminants that wheel hubs may encounter. In addition, the machine can simulate different temperatures, humidity levels, and other environmental factors to evaluate the wheel hub’s resistance to water and other contaminants.
Each hub assembly undergoes rigorous testing to ensure the bearings are sealed above market standards.
Salty spray testing
This test is designed to simulate harsh environmental conditions, such as exposure to saltwater, which can cause corrosion and deterioration of the components over time.
During the test, the wheel hub is exposed to a saline solution mist for a set period while placed in a controlled environment such as a testing chamber. The wheel hub is inspected for any signs of corrosion, such as rust or pitting, affecting the component’s performance and safety.
By subjecting wheel hub components to salty spray testing, we can evaluate the performance of the products in harsh environmental conditions and make necessary improvements to ensure that our products meet the required performance and durability standards. Ultimately, this helps to ensure the safety and reliability of the wheel hub assemblies used in vehicles, especially in areas where salt or corrosive materials may be present on the road surface, such as coastal areas.

Let's be great together
Unlock Your Competitive Edge: Inquire Now for Unmatched Wheel Hub Solutions!
We have been doing only one thing for the past 13 years. This is to “make good wheel bearings and hub assemblies”; we will continue to do this in the future.
More Advantages
Not all wheel hubs are the same; let’s talk about our stand-out.
High Grade Steel Bearings
Our bearings are high-strength GCR15 steel, subjected to a proprietary process to achieve maximum hardness, and finally treated with a G-10 finish.
High-grade GCR15 steel prevents premature failure due to extreme temperatures and high loads during normal operating conditions. G-10 resin is among the most challenging “glass fiber resins” available. Non-treated steel bearings showed signs of scoring after only a few thousand miles of simulated testing at various speeds. At the same time, treated steel bearings lasted over one hundred thousand miles of simulated testing.
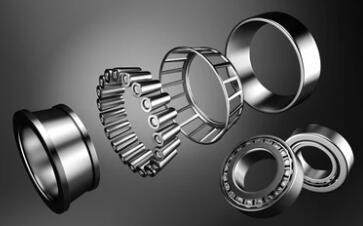
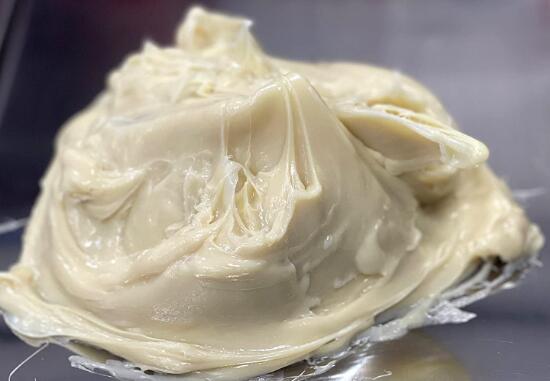
High-Quality Grease
We use Kyodo Yushi AFI grease, made in Japan and specially designed for wheel bearings; it has a long lifespan and performs well in extreme weather.
Without the grease, the best bearing in the world would fail very quickly. So, it’s essential to use high-quality grease that will last the life of the bearing.
Triple & Quadruple Lip Sealing
We use triple and quadruple lip sealing technology. This technique uses high-temperature-resistant rubber to achieve maximum bearing protection against dust, water, and road debris.
10/08F steel plates+NBR rubber.
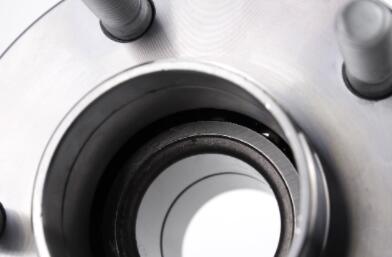
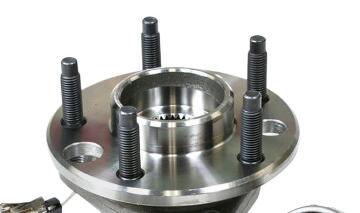
10.9 Grade Bolts
Our wheel hubs use 10.9-grade bolts; the pulling force can reach 1000 Nm, far exceeding the international standard of 750 Nm. This makes the quality of our bolts much better than other brands in the market.
OEM Specification ABS Sensors
ABS sensors used with our Wheel Hub Assemblies are manufactured with premium wire casings with 99.90% pure copper on the internal wiring for excellent electrical conductivity and optimal performance. In addition, our sensors are rigorously tested using the latest state-of-the-art equipment to ensure that the signal waves meet or exceed OE specs and Electromagnetic Radiation Detectors to detect noise to eliminate radio interference. The chip is imported from Germany.
The ABS Sensors’ sole function is to measure the rotational speed of a wheel and then transmit the collected information to the vehicle’s Engine Control Module (ECM) to assist the anti-lock braking system in controlling the cars driving stability under varying conditions. With premium wire casings, excellent electrical conductivity, and rigorous testing, we can ensure the high performance, durability, and longevity you expect for your vehicle.
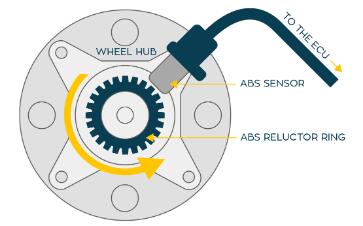
Our Certificate
IATF 16949:2016
Please see our IATF 16949:2016 certificate, which is another reflection of our strength; after all, not all wheel hub factories have the ability to obtain this certificate.
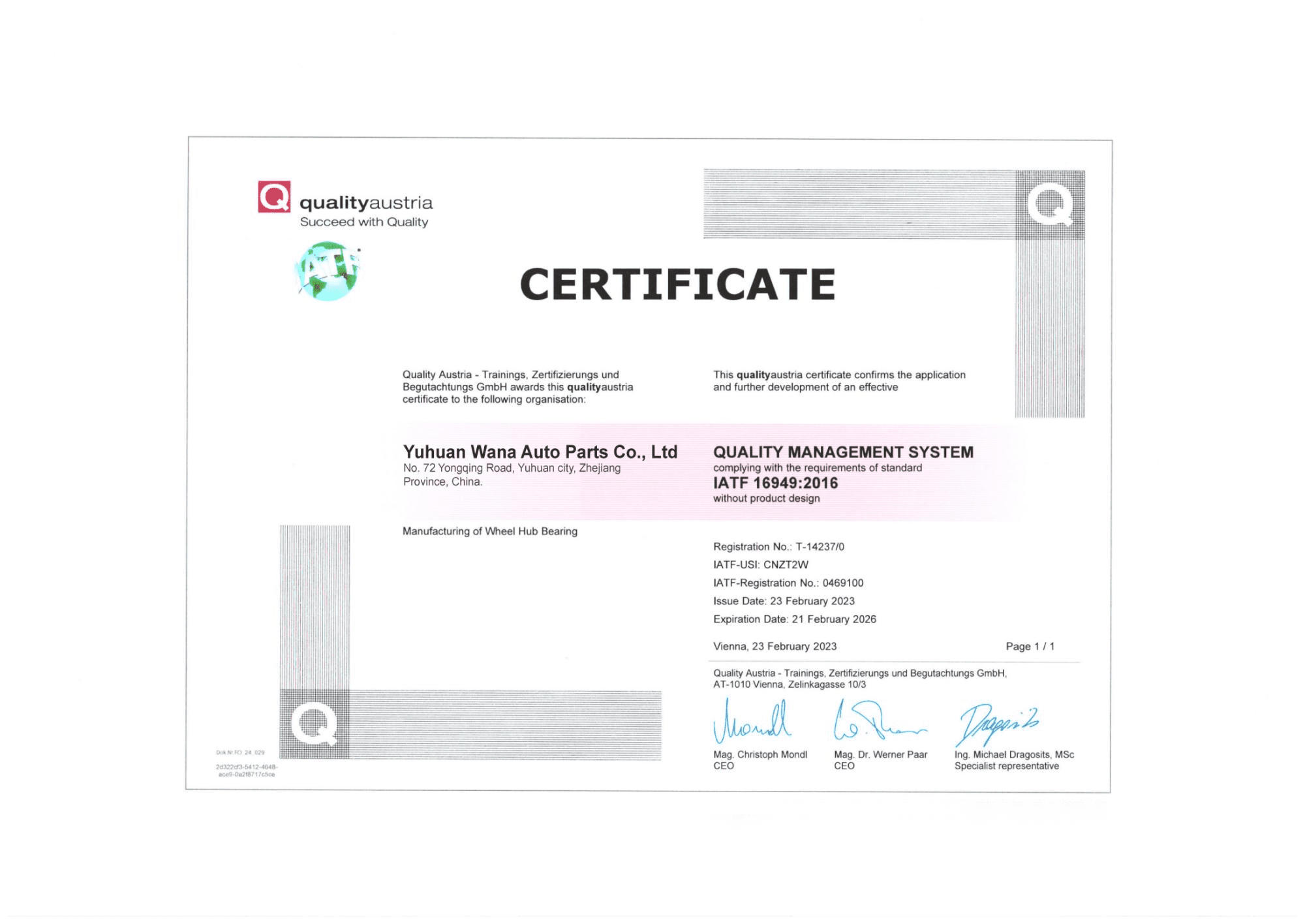
Our Awesome Customers
What Our Lovely Customers Says
Over the years, we have served over 200 foreign and over 150 domestic clients, and our products’ quality, service quality, and response speed have given a very high evaluation and praise rate of more than 99%! Here’s what they all have to say about us.
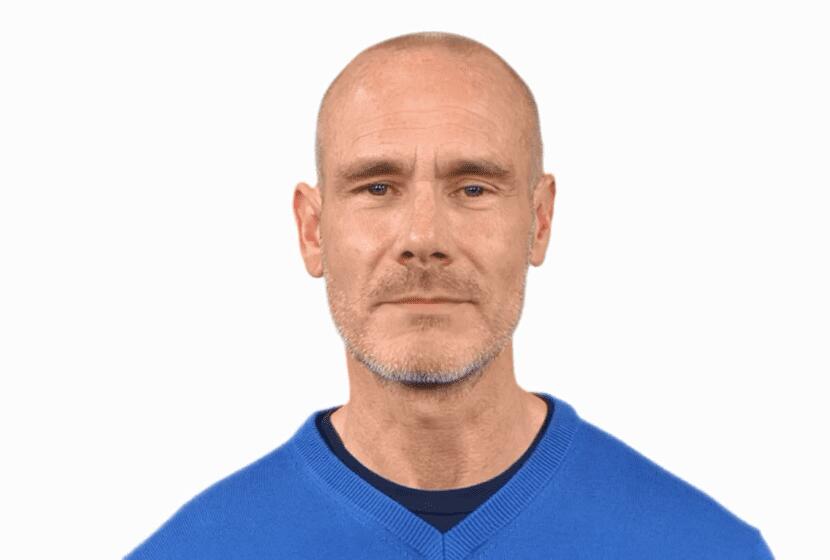
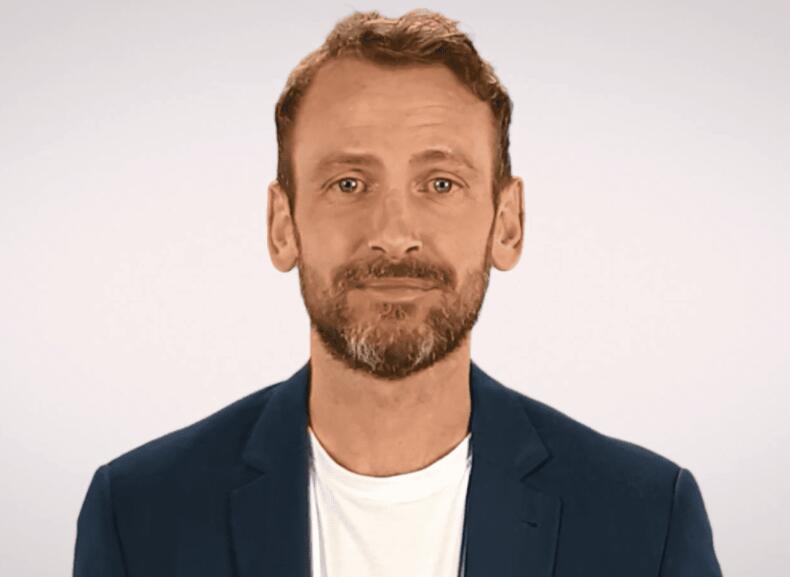
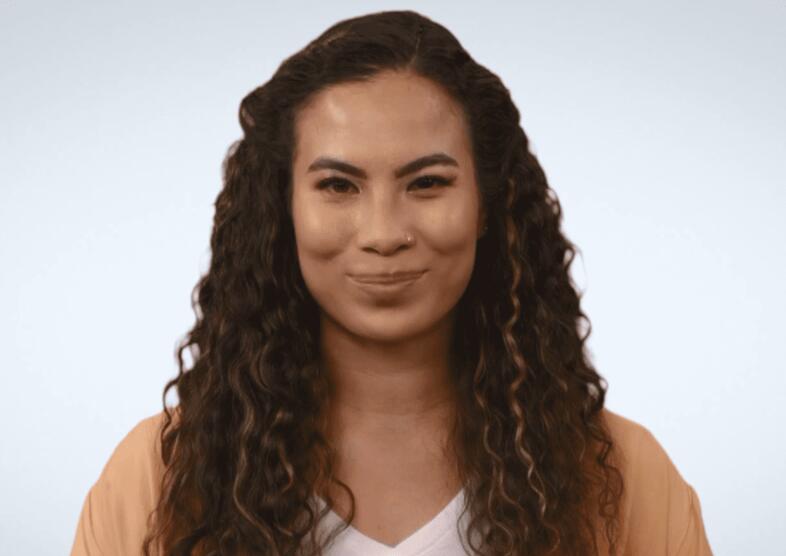
FAQ About Our Wheel Bearing And HUb Assembly
These are the most frequently asked questions. If you cannot find an answer here, please get in touch with us via email.
We are a family business manufacturing located in Yuhuan city, China’s largest automotive chassis parts zone. There are tens of thousands of factories of automotive chassis parts here. So you can find any chassis parts here.
Usually, the minimum order quantity is 200 pcs, because some models we have in stock, and for those we don’t have in stock, the minimum order quantity is 400 pcs.
We offer EXW, FOB, CFR, CIF, and Door to Door delivery terms. All subject to customer requirements.
Accurate factory price, no middle man.
Yes, we offer free samples for your test.
All products from Wana Auto Parts are covered with a 24 Months warranty from the date of installation or 80,000 km, whichever comes earlier.
- Check whether the product pictures are consistent.
- Also, verify that the product OE or standard primary manufacturer number is correct.
- Then, check if the applicable model and year are accurate.
- Finally, check if the product length and mounting dimensions are correct.
Any port in China is ok for us, but the most are Ningbo, Shanghai, Yiwu, Guangzhou, Qingdao etc.
- Pay 30% in advance and 70% before shipment by T.T.
- 100% payment before shipment by T.T.
- 100% payment aginst BL copy by T.T.
- 100% payment 30 days from shipping date by T.T.
Usually, for the models we have, the lead time will be less than 80 days; for newly developed products, the lead time will be 95 days.
All shipment products are documented, and we provide OEM services to many brands without any information about our manufacturer of the goods. Any drawings, operating instructions, test reports, etc., belong to the brand owner.
Yes, custom service is our leading service, tell us your requirements, and we’ll take care of the rest.
Yes, anything you need.
- Provide samples, and we will make drawings, or you can provide us with detailed production drawings.
- Then, make a mold and produce a few roughs.
- Produce pre-production samples and send them to you for confirmation.
- After your side approves the samples, we will start mass production.
- If you do not confirm the sample, we will make changes according to your requirements and resend the sample to you until you approve the sample.
- After the mass production, you can arrange for a third party to inspect the goods, or we will send you samples of large goods for your inspection.
- After you approve, we will ship your goods.
Who paid for the mold, and who owns the mold.